On the basis of having a whole small test equipment, in order to facilitate customers to come to our company to investigate the equipment, the company recently invested in the construction of a pilot production line, so that customers can understand the performance and characteristics of the equipment closely and intuitively.
This pilot line consists of the following equipment:
GHLZ-150 High-speed Stirring Wet Granulator (with Wet Granulator)
FLZB-20 Multi-functional Fluidized Bed
Mobile Dry Granulator
This line is capable of testing the following functional units
1. High-speed shear mixing granulation and drying, granulation unit
Adoption of equipment:
GHLZ-150 High-speed Stirring Wet Granulator (with Wet Granulator)
FLZB-20 Multi-functional Fluidized Bed
Mobile Dry Granulator
Granulation principle:
High-speed shear mixing granulation is by the stirring paddle to make the material regular three-dimensional movement, while the high-speed rotation of the cutting knife cut many times, so as to form a fine, uniform, rounded particles. High-speed shear mixing granulation, the main mechanism for nucleation and aggregation, when the powder surface contact with the binder (wetting agent) when the nucleation begins, the beginning of the liquid connection between the particles of the bridge is formed, the nucleus in the stirring paddles and cutting knives extrusion with the wet material aggregation, the particles merge to increase. Increased inter-particle fusion requires excess moisture on the surface of the granular object. This moisture comes from the continuous addition of a binder (wetting agent) or from the extrusion of moisture from the wet material to the surface of the granular material through continuous buildup.
In the granulation process, the growth process of the particles is accompanied by the crushing process due to the shear force. The dominance of the growth process and the crushing process is determined by the mechanical strength and shear force of wet granulation. The mechanical strength of wet granulation depends on the size of the initial particles; the magnitude of the shear force is related to the structure and rate of the mixing paddles and cutting knives.
Process description:
(1) According to the requirements of the process, the powder material is added into the material pot of the high-speed stirring wet granulator, and the material is mixed evenly in a short time through the movement of the stirring paddle and cutting knife.
(2) According to the requirements of the process, the binder or wetting agent will be conveyed into the material pot through the diaphragm pump and spray gun under the movement of suitable stirring paddles and cutting knives, and the suitable granules will be made through the movement of the materials under the joint action of centrifugal force, gravity and the mechanical force of stirring paddles and cutting knives.
(3) According to the requirements of the process, the larger lumps in the wet particles will be broken up by the suitable screen, gap and rotating speed of the wet granulator, and the wet particles will be transported to the fluidized bed for drying through the gravity of the wet particles and the negative pressure of the fluidized bed.
(4) According to the requirements of the process, dry the wet particles under the appropriate air inlet, air inlet temperature and air inlet humidity until the process requirements are met, and discharged.
(5) According to the requirements of the process, the dried particles will be pelletized through the suitable screen, gap and rotating speed of the dry pelletizer.
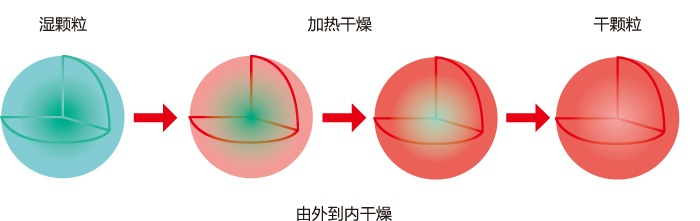
2. Fluidized bed one-step granulation unit
Adoption of equipment:
FLZB-20 Multifunctional Fluidized Bed
Mobile Dry Granulator
Granulation principle:
In the fluidized bed, compressed air and binder liquid in accordance with a certain ratio by the gun atomized and sprayed to the fluidized bed is in the fluidized state of the powder material. The granulation process includes three stages: mixing, granulation and drying. First of all, the liquid droplets make contact with the powder wetting and aggregation around the formation of particle nuclei, and then continue to spray into the liquid droplets fall on the surface of the particle nuclei to produce adhesive bridging effect, so that the particle nuclei and particle nuclei, particle nuclei and particles combined with each other, and gradually form larger particles. After drying, the liquid bridge between the powder gradually become solid bridge, this process is repeated, that is, the ideal, uniform, rounded shape of the porous spherical particles. Because the fluidized bed granulation process is not subject to external forces, only by the influence of airflow in the fluidized bed, so the resulting particles are small density, low particle strength, but the particle size is uniform, mobility, compression molding properties of the number.
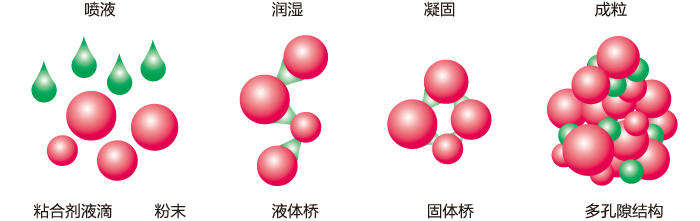
Process Description:
(1) According to the requirements of the process, the powder material is added into the fluidized bed material chamber, and the powder material is aggregated and bonded under the suitable air inlet, air inlet temperature, atomization pressure, liquid spraying speed, air inlet humidity, and material temperature, until it meets the requirements of the process, and is discharged.
(2) According to the requirements of the process, through the dry granulator suitable screen, gap and speed of dry particles granulation.
3. Fluidized bed bottom spray coating unit (Wurster system):
Bottom spray coating principle:
The Wurster system, invented by Dale Wurster, a professor at the University of Wisconsin, is an important breakthrough in coating technology, which makes it possible to coat materials with small particle sizes and plays an important role in promoting the development of micro-pellet technology. It involves installing the spray gun at the bottom of the fluidized bed, facing upwards and in the center of the deflector barrel. Through the separation of the deflector cylinder and the venturi effect produced by different airflow distribution plates, the material moves upward from the deflector cylinder, spreads in the upper part of the deflector cylinder, and falls down from the outside of the deflector cylinder under the action of its own gravity, and flows into the deflector cylinder at the gap between the bottom plate of the fluidized bed and the deflector cylinder to realize the orderly cyclic movement. The direction of the atomized liquid droplets into the fluidized bed is the same as the direction of the fluidized gas, and it is in close contact with the material, which can reduce the loss of the atomized liquid and improve the coating efficiency. It can also effectively prevent the particles from gathering and sticking. With the development of technology, it has been possible to coat powders as small as 50μm.
Features of the Wurster system:
(1), the material can be highly dispersed and accompanied by coating film spraying without adhesion;
(2), the distance of the fog particles to reach the material should be very short, the wet points without rapid evaporation, and the material to produce a good adhesion, and has a very strong spreading, making the film firm, continuous;
(3), the material and fog particles should be equal contact opportunities, uniform coating;
(4), consume less coating material, and uniform coating film.
Process Description:
According to the requirements of the process, the micro-pellets or particles will be added to the bottom of the fluidized bed spray material chamber (be careful not to add to the guide tube), in the appropriate air inlet, air inlet temperature, atomization pressure, spray liquid speed, air inlet humidity, material temperature under the addition of micro-pellets or particles for spraying until the process requirements are met, discharged.
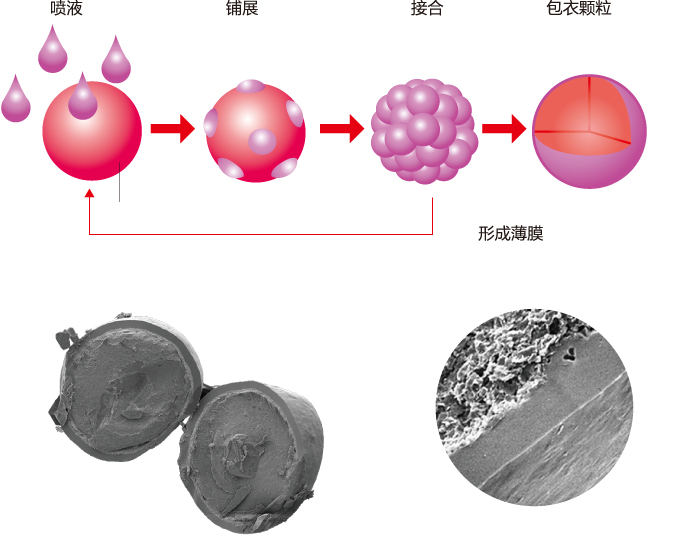
4. Production capacity of the line
GHLZ-150 High-speed Stirring Wet Granulator:Effective working volume 55~144L
FLZB Multi-functional Fluidized Bed: Effective working volume of top spray 12~45L
Bottom spraying effective working volume 8~38L
Welcome all the honorable customers and experts to visit, test and discuss.